Back to articles
Machine Learning is transforming the Industrial Internet of Things
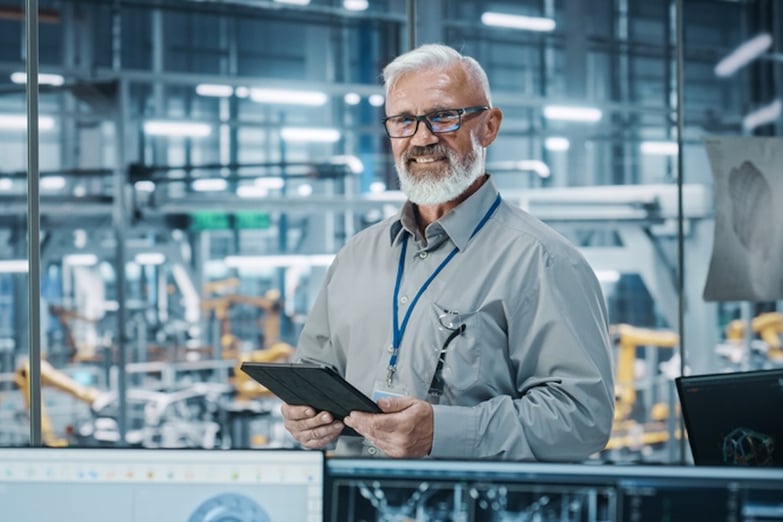
‘Industry 4.0’—the next stage of the Industrial Revolution—leans heavily on the Industrial Internet of Things (IIoT) to support large scale automation of traditional manufacturing practices. In turn, today’s IIoT is founded on wireless machine-to-machine (M2M) communication, edge computing, and Machine Learning (ML).
Wireless networks using these technologies link machine tools, programmable logic controllers (PLCs), sensors, gateways, and the Cloud, enabling every part of the factory to gather and process data and share information with every other part as well as the Internet. This deep mine of information is enabling engineers to revolutionize how everything is manufactured - from cans to cars, screws to smartphones, and jigsaws to jet turbines.
But there is always room for improvement. For example, machines can be further enhanced to improve yield and quality while using less material, while engineers can design products for greater sustainability. A new generation of IIoT solutions promises to make this happen.
IIoT and M2M increase manufacturing flexibility
Wireless technology not only cuts the cost of implementing IIoT connectivity it also makes it easy to reconfigure networks as the factory adapts and expands. Such technology not only changes the way products are made but also how they’re designed.
Now, connectivity links the front office to the factory floor using M2M communications, allowing computer aided design (CAD) tools to talk to machine tools to directly program them to make parts. And machine tools can speak to CAD to let them know where the bottlenecks are in the manufacturing process such that products can be redesigned for simpler manufacture without compromising function.
The results are an increase in productivity and reduction in product failures - bringing sustained cost savings and environmental benefits.
Edge computing and ML optimize production in smart factories
Once mass production is up-and-running, wireless technology makes the modern factory a highly controlled and optimized environment. Things rarely go wrong. But rarely doesn’t mean never. Today’s wireless Bluetooth LE Systems-on-Chip (SoCs) from Nordic incorporate powerful embedded processors to perform edge processing, looking for the infrequent trends that indicate things might be changing for the worse. This edge computing is increasingly reliant on ML models constantly adapting to spot deviations in sensor trends and forwarding the key information for further action.
Such models can help to pre-empt issues that might arise due to these external factors—for instance, an increase in humidity caused by workers arriving for the day, air flow from open windows and doors, and changes in temperature throughout the day and night—and adjust machine settings in advance of those factors impacting manufacturing processes. And dedicated vibration and acoustic sensors can monitor the machine tools to make sure they are in the best of health. Any unusual vibration, temperature increase or increase in power consumption can be reported ahead of a breakdown for early maintenance – thus preventing an unscheduled and expensive hiatus in production.
- Read more: Artificial intelligence and machine learning will transform the IoT
- Read more: Remote industrial monitoring provides critical data and insights
Tech to power the industrial future
But while modern factories are impressive examples of the power of connectivity, standing still is not an option. The Japanese concept of Kaizen (“improvement”) epitomizes this strategy. Kaizen guides continuous effort across the factory to improve programs and processes while eliminating waste and redundancy. Kaizen has proved so successful that it has spread throughout the world.
To continue the improvement process, factories will need even better wireless technology than they have today. Nordic is working hard and investing deeply to build and supply the next generation of IIoT technology. Several multiprotocol SoCs and Systems-in-Package (SiPs) from Nordic’s product range already support TinyML, a framework for running embedded ML on constrained devices. But there’s much more to come.
The company’s new nRF54H20 SoC, for example, integrates multiple Arm Cortex-M33 processors, clocked up to 320 MHz, together with multiple RISC-V coprocessors. The higher clock speeds of the SoC’s application processors allow for reduced processing latency for AI operations, when compared to Nordic’s nRF5340 SoC.
Better yet the nRF54H20 brings increased efficiency—cutting the power consumption required to run equivalent operations—because it is fabricated using the cutting-edge 22-nm process node. In addition, Nordic’s next-generation multiprotocol radio offers improvements in both TX power and RX sensitivity, enabling efficient and reliable transfer of information from embedded ML applications to Cloud connected devices, or between different nodes in a network. This makes the SoC ideal for next generation IIoT applications.
The nRF54H20 will be supported in Nordic’s ML Studio alongside the nRF52, nRF53, nRF91 Series products already supported.
The beginning of a revolution
Wireless tech is booming in IIoT applications. According to ABI Research, the Bluetooth-enabled industrial devices market alone is expected to grow from 143 million annual unit shipments in 2023 to over 611 million by 2028, achieving a CAGR of 34 percent over the five-year forecast period[1]. But even with this impressive growth things are just getting started; Industry 4.0 is set to have a larger impact on global manufacturing than all three previous major leaps in the industrial revolution combined.
References
1. https://www.abiresearch.com/market-research/product/7783366-how-can-bluetooth-technology-enable-digita/